Other
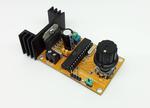
“This DC Motor controller provides direction and speed control of brushed DC Motor using Rotary Encoder. This is Arduino compatible hardware that consists of LMD18201 DC motor driver chip, Atmega328 microcontroller, Rotary Encoder, L317 regulator, and other components. Hardware offers …
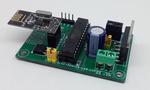
“This is Arduino compatible hardware that can control a single DC motor speed, direction, and brake using an RF remote control. The project is based on an ATMEGA328 microcontroller, H-Bridge DC motor driver chip LM18201, NRF24L01 RF module, 5V Regulator …
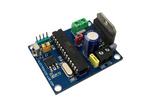
“This project enables the user to control a Brushed DC Motor using an Infra-Red Remote Control, thus controlling speed, direction, and also brake of DC Motor is possible. It’s an Arduino compatible open-source hardware that helps you develop many …
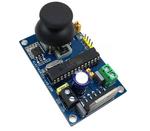
“This DC Motor controller provides direction and speed control of a brushed DC motor using a Joystick. This is an Arduino compatible open-source hardware with various applications. It can be used to control scissor lift motor, Linear actuator, Camera slider …
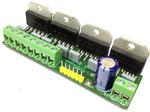
“This compact board will help you to drive 4 Wheel Drive Robots, each axis can handle a load current up to 3 Amps and supply 12V – 48 V DC. Board requires two PWM and Dir. signals for full 4WD operations …